Whenever, we buy equipment, the next stage is back to the boat for more work…..the job list does not seem to get any shorter and every job takes much longer than expected.
Freezer
Those of you who have been reading our previous blogs, will know that one of our earlier jobs was to get a freezer fitted. Fox’s boatyard did an amazing job of building us a new cupboard and shelves in the aft (back) cabin to house this. We had hoped that this would cross a job off the list…..unfortunately this was not the case.
After a few weeks of use, we noticed that the bottom shelf was turning black. This is a sign of moisture creeping into the wood. On further investigation, we found that the outside of the freezer was running with condensation. This in turn was tracking across the wood to the shelving. Not good.
We researched the problem and possible solutions….we needed better ventilation, better insulation and a drip tray to catch any water. This meant the freezer and all of the new woodwork needed to come out!
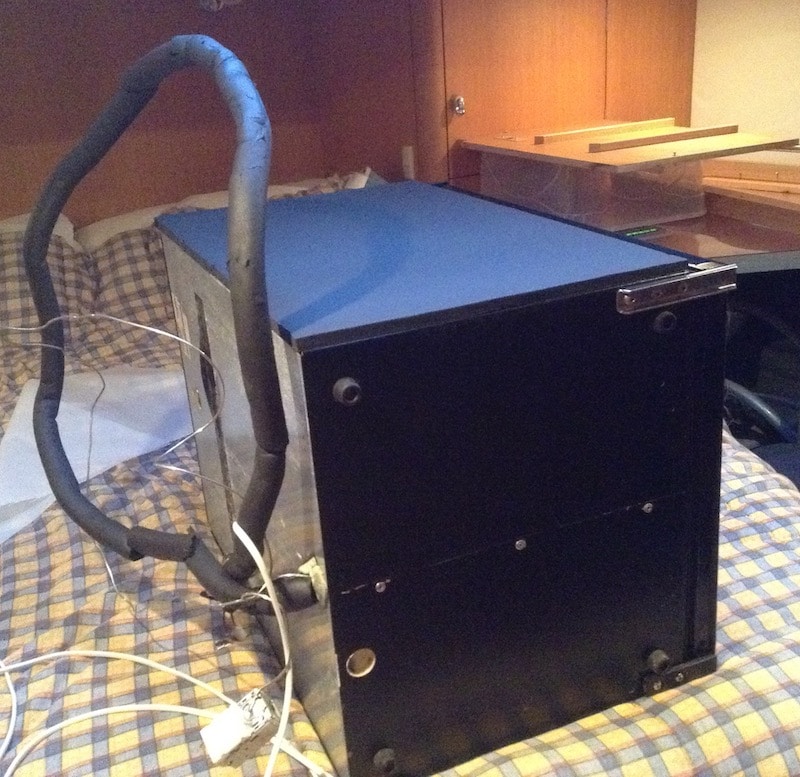
Electrics
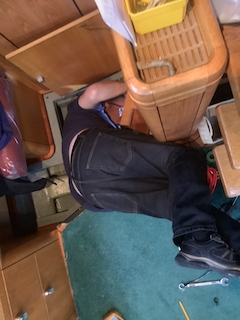
Another massive job is to update the electrics. We have added a lot of additional equipment – davits, generator, freezer, new communication equipment…. All of these require electricity to run, so need new cables from where they are installed back to the batteries. Sounds simple? Maybe in a house, but not on a boat. The cables run under or behind other things and usually require you to be a contortionist to reach them!
Lockers
Many of the jobs on the boat require specialist skills and knowledge. Some of these things we have had to get others to do, but many we have learnt about ourselves. Martin tends to do the technical stuff. I, on the other hand, do the unskilled, manual labour! Very different from my previous life as a headteacher.
One of my biggest jobs is to sort out the stowage (storage) on board: finding homes for everything and remembering where it all is. As part of this, I decided to re-line all of the lockers (cupboards). When we bought the boat, they still had the original lining fabric in them and were looking very tired and, in some cases, mouldy.
First job was to strip them: a very messy job as the fabric was self adhesive and the foam backing had disintegrated. Also the lockers are small and strange shapes, so squeezing into them required flexibility!
After stripping and cleaning them, the next job was to recover them. After much research, we decided to use rubber carpet underlay against the hull (helps with insulation) and then car carpet over the top. This was ideal as it is self adhesive (so no glue fumes) and stretches four ways (so covers the uneven surfaces). There are 20 lockers on board to do, so this has been a long job! I am hoping not to have to do it again!!

Kobi and I are really enjoying uour posts x
Hi
How are you all? I can’t believe Kobi is half way through his first year at JW already. Hope it is going well.
Thank you for the message. It is so good to know that you are reading the posts and enjoying them. The countdown is really on now as we are planning to leave the boatyard in April. Then we will spend some time on the south coast, hopefully going across to the Channel Islands. The big departure is planned for June when we head towards Portugal and beyond…
Caron x
Excellent blog Caron, I guess that was Martin’s arse in the photo, we dont realise that condensation with freezers occurs because the equipment these days deal with it but when enclosed that’s an issue good you found it early on, I doubt your missing the teaching, what’s it like working for a living 🤣🤣🤣
Hi,
Yes it was Martin, although there are very similar photos of me!! Most jobs seem to require working like this.
I am really enjoying the ‘work’ although it can be very frustrating at times when things don’t go according to plan.
As you know Martin is still working at his proper job, so his boat work is restricted to evenings and weekends!!
See you both on Wednesday.
Caron x